Averting Disaster with Superalloys
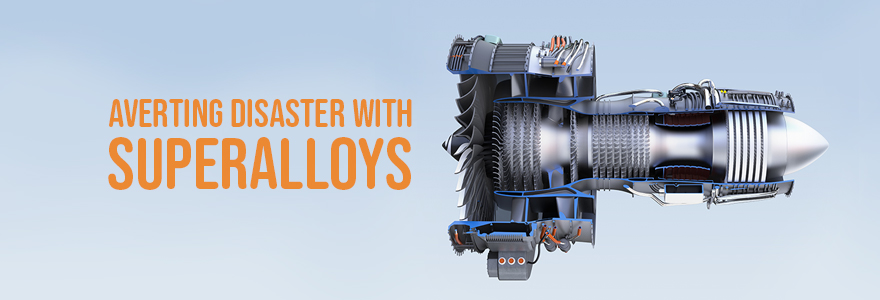
Whether jetting off on vacation or driving across a bridge to get to work, most of us would agree that our top priority is to arrive at our destination safely. We may get nervous as our flight barrels down the runway or feel dizzy prior to crossing a bridge. We try not to think about the worst-case scenario, but are certainly aware of the ultimate result of the risk being taken.
A jet engine is produced with a variety of alloys, metals made by combining two or more metallic elements, to give them greater strength and resistance to corrosion. Other every-day applications of these compounds range, from the steel in cooking equipment to the brass in doorknobs. Such materials, however, can fail under severe conditions like extreme pressure or temperature and they may experience metal fatigue from repeated use. For example, see the image (right) of a corroded surface of an Ni-based alloy. It shows a transition from an undamaged area that progresses into a more heavily damaged area.
Everyone – government officials, industry magnates, and individuals like you and I – grapple with the notion of accepting risk every day and in everything we do. Given the high stakes associated with material failure in products like jets, gas turbine engines, and nuclear waste storage units and the incontrovertible need to ensure public safety, the design of novel super-materials is critical to averting the type of disaster from which it may be impossible to recover.
Enter PhD candidate Jeffrey D. Henderson with Western University’s Electrochemistry and Corrosion Science Group (ECS), who is focusing his research on better understanding the structural behaviour of nickel-based “superalloys.” Designed to provide greater strength at high temperatures and superior corrosion resistance than can be achieved from iron or steel, this nickel-based material presents the unique industrial advantage of surviving in the harshest of mechanical, chemical, and physical environments.
Even these materials, though, have a ‘shelf-life.’ How long will a nuclear waste container, buried deep in the ground resist corrosion; 100, 1,000, or perhaps 10,000 years? Consider that used nuclear fuel can remain radioactive for up to 1 million years. “It is crucial to understand more about the corrosion performance of the superalloy used in this and many other applications to avoid potential environmental contamination and the significant financial and human costs this could entail – today and far into the future,” stresses Henderson.
Henderson has developed new techniques to reveal the role that individual alloy components play in preventing material degradation. This information is crucial when designing metal blends to withstand particularly severe conditions. He has discovered how a specific element, molybdenum, can help stabilize the protective film formed on nickel alloys. The inside of a commercial jet engine reaches temperatures hotter than molten lava; over time, this constant thermal strain may cause the protective metal film to break down. Fortunately, the properties of nickel alloys allow the engine to complete about 20,000 flight hours before it requires significant maintenance.
Henderson will soon make these discoveries available to the scientific community, so researchers can continue to develop optimal alloy compositions. Ultimately, industries could rely on these enhanced versatile metals to avoid out-of-pocket reparations - or even threats to public safety - that would ensue from frequent material failure. For now, his lab mates at Western University are benefitting from his findings as they design nuclear fuel containers that must withstand material decay for generations to come.
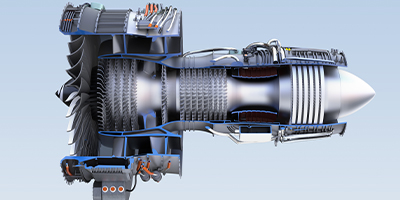
Jet engines with major components fabricated from high-performance Ni-based superalloys can withstand extreme conditions.
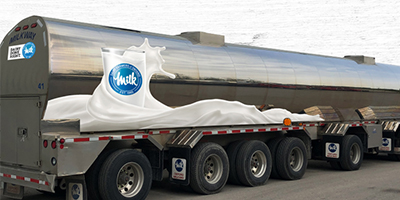
Tanker truck for collection of milk from dairy farms, made of food-grade Ni-bearing alloy with low corrosion rate avoids contamination of the milk with metal ions.
Story written by Jessica Singer.